The client → Confidential Client
What was assembled → Nozzle Actuator of a Print Head onto the Ink Manifold
CASE STUDY
Do you want to learn more about this project?
The Challenge
The requirement for this project was to assemble the nozzle row and first nozzle of the print head with under 3 µm accuracy. This must be applied in all dimensions towards a mechanical and conical reference feature of the manifold. As the tiny nozzle holes are used as the reference point, alignment through mechanical referencing was not an option. In fact, simply touching the nozzles was not permitted due to their fragile nature.
A custom designed vision systems was the most efficient way to detect the nozzle holes and align them against the mechanical reference system.
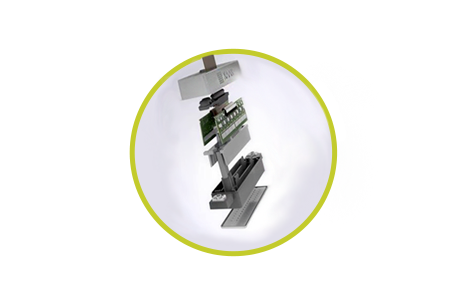
"Our client is no longer reliant on the outside boundaries of parts. This allows them to use less expensive components, but produce better product with an accuracy level of less than 3µm."
Kurt Hensen
Vice-President, Business Development
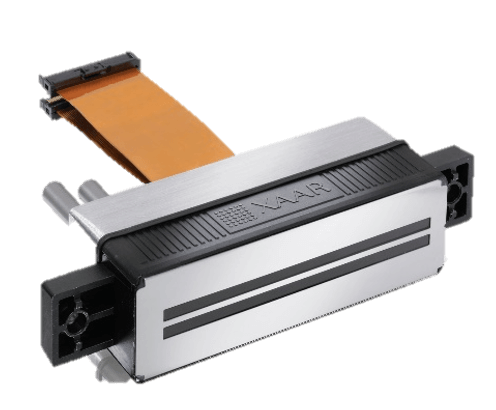
The Solution
To address the challenges of this application, the most efficient and effective solution was to leverage passive assembly with vision-in-the-loop feedback. As physical features are used to align the 2 parts and no components are activated, active alignment is not required.
To lock the 2 parts into place, a combination of UV curing and thermal curing adhesives were used. This was automatically applied, and all parts are fully automatically assembled.
By working with a passive assembly station with vision-in-the-loop feedback, the focus remains on product reliability and high-quality delivery.
Results & Benefits
- 3µm accuracy towards mechanical references.
- Increased production volume.
- Minimal reliance of parts tolerances, allowing for better value per component.