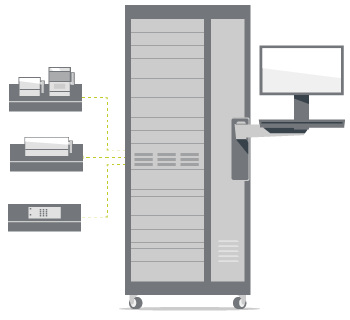
テストで次のステップに進む
テストプロジェクトを進める前に、投資に対するリターンを理解することが重要である。自動テストのコンセプトを理解し、なぜそれを使うのか、いつ使うべきなのかを理解することで、それを財政的に正当化することが容易です。
製品テストを成功させることは品質に不可欠であるが、それにはコストもかかる。テストを手動にするか、自動にするか、あるいは両方を組み合わせるかは、多くの要因に基づいて決定される。意思決定者は、最新のベストプラクティスだけでなく、高レベルのコストドライバーを理解する必要があります。
続きを読む:
自動テストの歴史
手動テストと自動テスト
自動テストの種類
手動テストと自動テストの選択:
アプリケーションは自動化に適しているか?
自動化は財務投資に値するか?
自動テストの定義
自動試験とは、コンピュータが製品に対して一連の個別試験を論理的な順序で実行できるようにするプロセスである。これらの試験は、計測器ハードウェアを使用して計測を行い、計測値をあらかじめ定義された限界値と比較し、製品が合格か不合格かを判定する ソフトウェア(テストエグゼクティブ)を備えたコンピュータに送信します。自動化を利用することで、試験手順を非常に迅速に、確実に、繰り返し実行することができ、ヒューマンエラーのリスクも限定されます。自動テストは現在、エレクトロニクスを使用するあらゆる産業で使用されており、自動テスターの数は大幅に増加しています。
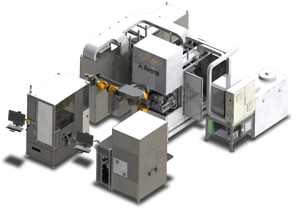
自動テストの日常的な例
手動テストから自動テストへの移行の 一般的な例は、地元の整備工場で見ることができる。車の修理が簡単だった頃、消費者は整備工場に車を持ち込む。整備工場では、ディストリビューターやスパークプラグ、キャブレターに燃料が供給されているかどうかといった項目を手作業でチェックしていた。これらのチェックは、故障が診断され修理が実施されるまで、一度にひとつずつ行われた。最近では、整備士は自動車をコンピューターに接続してボタンを押し、コンピューターがより包括的な測定を行った後に生成されるテスト結果を分析する。例えば、エンジン・コントロール・ユニット(ECU)のテストでは、多くのテストが、メカニックが正確に何が起こっているかを知る必要さえなく実行される。このプロセスは自動テストと定義され、一連のテストが製品に対して順次実行される。
自動テストの歴史
製品の複雑さはさまざまであり、試験方法もさまざまである。多くの場合、製品が複雑であればあるほど、製造とテストにかかるコストは高くなります。自動試験装置(ATE)は、最初のプロトタイプ開発から最初のバッチ試験、そして最終的には完全生産に至るまで、製品開発のライフサイクル全体を通じて使用されます。同じテストシステムが、修理ステーションや製造委託先で使用されることもよくあります。製造場所にかかわらず、試験装置は一般的に企業の研究開発センターの近くで設計・開発される。これは、エンジニアが製品をテストする最善の方法について最初のアイデアを共有し、テストするための費用対効果の高いソリューションを考え出すことができるようにするためである。
多くの場合、試験開発エンジニアが装置を設置し、現地オペレーターに装置の使い方を指導して、最大の性能を引き出す。どの試験装置を使用するかは、一般的に製造される製品の種類によって決定される。歴史的に、ATEは高価で、プログラムも難しかった。主にミッションクリティカルな製品に使用されていた。初期のテスト機器は「ラック&スタック」として親しまれており、その名の通り、ラックベースのテストシステムで、個々の測定器がたくさん積み重ねられていた。これらは、1960年代にヒューレット・パッカード社が発明したGPIB(General Purpose Interface Bus)で接続されることが多かった。GPIBは8ビットのパラレルバスで、ソフトウェア開発者がユニークで直感的なアドレッシングシステムを通じて、個々の計測器をアドレス指定できるという利点があった。そのため、ソフトウェア開発者は、どの計測器をどのような順序で制御し、いつ検査結果を返すかを決定することができた。GPIBはテストシステム設計に革命を起こし、昨今でも広く使われています。
テスト機器は、PCI、PCI Express、PXI、イーサネット、USBなど、より高速なバスによって、過去30年間で飛躍的に進化しました。これらの新しい規格は、試験装置の計測器とコンピュータ間のデータ転送を大幅に高速化します。その結果、自動試験装置は大幅にコストを削減し、性能を向上させた。現在、完全に機能するATEは、1980年代以前には数十万ドルもしたのに比べ、数千ドル程度で手に入ります。価格の低下と技術の向上により、あらゆる企業でATE導入が急増している。かつてはミッションクリティカルな製品のみをテストする領域であったATEシステムは、現在ではほとんどのハイテク製造企業で一般的なものとなり、低コストから高価値までさまざまな製品を生産している。
手動テストと自動テスト
手作業による試験工程は通常、1人または複数の個人によって行われ、試験が完了するまで、1つの測定作業に続いて別の作業を行う。一日中試験装置の前に座り、計測器を見ながら試験結果を書き留めるオペレーターを雇っている企業も少なくない。このプロセスは長年使われてきており、人件費が安い場合には使われ続けている。手動試験は、製品の試験プロセスが極めて単純で、オペレーターが短時間で試験を実施できる場合にも使用される。一方、自動試験は、コンピューターベースの試験システムが製品の試験プロセスを実行する場合である。歴史的に、自動試験装置は高価で複雑なものであり、ほとんどの自動試験システムは防衛、自動車、電気通信産業向けに作られたものであった。1970年代から1990年代初頭まで、コンピュータのコストは労働力に比べて非常に高く、その間、自動試験装置のコストは労働力をはるかに上回っていた。そのため、手作業によるテストが依然として主流であった。
テスト・シーケンスとテスト・エグゼクティブ・ソフトウェア
個々のテスト(テストモジュールと呼ばれる)は、特定の機能や検証を実行する。これらの個々の試験をまとめると、試験シーケンスと呼ばれる。テストシーケンスの例としては、(1)電源投入テスト、(2)電圧チェックテスト、(3)電流テストの順となる。自動化された試験装置では、複数の試験シーケンスを作成し、同一システム内で多数の製品の試験を容易にすることができる。テストモジュールは多くのプログラミング言語で作成できるが、テストシーケンスは通常、テスト実行ソフトウェアツールによって作成される。テスト・エグゼクティブ・ツールには、個々のテスト・シーケンスの作成、合格/不合格条件を決定するための測定限界の組み込み、測定値に基づいて新しいテスト・シーケンスを呼び出すことができる条件の作成など、多くの機能があります。この種のソフトウェアは、試験データを出力するためのフレームワークも提供し、結果をデータベースにアップロードしてさらに分析することができます。
半自動テスト
手動テストと自動テストについて考えるとき、白か黒かで考えないことが重要である。多くの企業は、テスト戦略に半自動テストと呼ばれる第3の選択肢を用いる。このオプションは通常、製品がテスト中に何らかの設定を必要とする場合に導入される。半自動試験とは、試験サイクルの一部または全部にオペレーターが立ち会うものである。製品は通常、コンピュータに接続された治具に設置されます。試験手順中、コンピュータ画面に表示されるグラフィカル・ユーザー・インターフェース(GUI)は、製品に対して何らかの手動調整が必要な試験手順の部分を通して、オペレーターをガイドします。これは、ポテンショメーターの調整や特定の機械部品の位置合わせを意味します。オペレーターが調整をしている間、コンピューターはパラメーターを読み取ることができます。値が必要な範囲に入ると、コンピューターはオペレーターに正しく設定されたことを表示します。これらのテストが実行されると、再びコンピューターが引き継ぎ、残りのテストは前述と同じ方法で完全に自動化されます。
自動テストの種類
自動テストシステムは、あらゆる専門分野を活用し、あらゆる形や大きさで提供されています。光学、RF、機械、電気、ソフトウェア、その他の専門家が、さまざまなテスト・プロジェクトのさまざまな場面で必要とされます。
テストの種類の例としては、以下のようなものがある:
インサーキットテスト(ICT)
インサーキット・テストの歴史は長く最初の用途は、電子製品に使用される個々の回路基板をテストすることでした。電気プローブは、プリント回路基板(PCB)をテストし、ショート、オープン回路、抵抗、静電容量、およびアセンブリが正しく製造されたかどうかを示す他の基本的な要素をチェックします。テストは、「ベッド・オブ・ネイルズ」と呼ばれるテスト治具と専用のテスト機器を使って行う場合と、治具のないインサーキット・テスト・セットアップを使って行う場合があります。ベッド・オブ・ネイル・テスターは、ガラス布をラミネートしたシートの穴に多数のピンを挿入した伝統的な電子治具である。ピンは、PCB上のテスト・ポイントに接触するように工具ピンを使って整列され、そのピンはワイヤーやケーブルで測定ユニットに接続される。小さなバネ付きピンはそれぞれ、被試験デバイス(DUT)の回路内の1つのノードに接触する。DUTをベッドオブネイルに押し付けることにより、DUTの回路内の数百あるいは数千の個々のテストポイントに対して、信頼できる接触を迅速かつ同時に行うことができる。押さえつける力は、手動または真空によって与えることができ、これによりDUTを釘の下方に引き下げることができます。ICTシステムには多くの場合、テストデータのロギングが組み込まれており、メーカーの設計に基づく独自の出力レポートが用意されています。多くのICTシステムは現在も使用されていますが、徐々に以下に説明するバウンダリースキャンシステムに取って代わられつつあります。ICTには、テストのスピードやPCBの多くの部分を同時にテストできる能力など、多くの利点があり、また既製品として入手できます。ICTは通常、サブアセンブリに組み立てる前に、個々のPCBをテストするために使用されます。
バウンダリー・スキャン
バウンダリスキャンは、近年非常に普及している自動テストの一形態である。JTAG(Joint Test Action Group)、あるいはIEEE標準規格(IEEE 1149.1)として知られるバウンダリ・スキャンは、従来のテスト形態に比べて多くの重要な利点を備えているため、最近の自動テストでは主要なツールの1つとなっている。バウンダリスキャンテストが開発された主な理由は、テスト用の基板や集積回路へのアクセス不足という問題を克服するためであった。製品が小型化するにつれて、利用可能な領域を見つけることが難しくなり、従来のテスト方法が適さないか、不可能であったことを意味する。バウンダリ・スキャンは、基板に実装された大型集積回路に特定のバウンダリ・スキャン・レジスタを持つことで、これを克服する。基板をバウンダリースキャンモードに設定すると、集積回路内のシリアルデータレジスタにデータが渡される。このシリアル・データ・チェーンからのレスポンスとデータの受け渡しにより、テスターは比較的高速に故障を検出することができる。バウンダリ・スキャンは、物理的なテスト・アクセスが非常に限られている基板や集積回路でもテストできることから、広く使用されるようになり、その使用は増え続けている。
自動光学検査 (AOI)
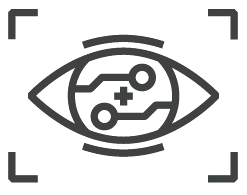
AOIは多くの製造現場で一般的である。基本的には目視検査の一種であるが、カメラ、コンピューター、ソフトウェアを用いて自動的に行われる。検査が自動化されているため、従来の手動検査に比べ、再現性とスピードが格段に向上します。AOIは、はんだ付けされたプリント基板を製造する生産ラインの最後に位置する場合に特に有用であり、はんだ付けの欠陥を含む製造上の問題を素早く特定し、正しい部品が装着され、その向きが正しいかどうかを判断することができます。この種の検査は従来、同じ種類の基板を何時間もかけて見るオペレーターによって行われていた。手作業による目視検査の最大の問題のひとつは、オペレーターの疲労である。シフトの終盤になると、手作業による検査の精度が低下し、不良品が合格したり、良品が不合格になったりすることがよくある。AOIはこれらの問題にうまく対処している。AOIシステムはコストが高いため、大量生産ラインでのみ使用されることが多い。
自動X線検査(AXI)
AXIはAOIと類似点が多い。しかし、BGA(Ball Grid Array)パッケージの出現により、光学的に見えないものを見ることができる検査形態を作り出す必要があった。AXIシステムは、医師が骨折の可能性を探すために骨のレントゲンを透視するのと同じように、はんだ接合部を正確に評価するために集積回路(IC)パッケージを透視することができます。
機能的自動試験装置
機能試験とは、その名の通り、機器の機能を試験するものである。これは、製造工程のずっと先で行われ、製品が梱包されて顧客に出荷される前の最終テストであることが多い。製品がこの段階のテストに達すると、何か欠陥が見つかった場合、通常、修理に最も費用がかかります。問題や設計上の問題は、テストして早く見つかれば見つかるほど、解決にかかる費用が少なくなります。ほとんどの機能試験機は特注品でなければならない。これは、その企業の製品のほとんどの機能がその企業独自のものであるという事実による。新製品が設計され製造される場合、多くの場合、これまでになかった機能が搭載されるため、その機能に対応したテスターは誰も作ったことがないのです。
組み合わせテスト
すでに説明した試験の種類を見ればわかるように、単一の試験方法で完全なソリューションを提供できるわけではありません。この問題を克服するために、多くのATEシステムは、1つのテスター内にさまざまなテストアプローチを組み込んでいます。テスト機能を組み合わせることで、テストカバレッジははるかに高くなる。また、組み合わせ型テスターは、ボードをテスターから別のテスターに物理的に移動させることなく、さまざまな種類のテストを実施することができます。この単一のテスト・スイートには、機能テストやJTAGバウンダリー・スキャン・テストだけでなく、ICTテストも含まれる。説明した自動テストにはそれぞれ長所があるため、必要なテストに適したテスト手法を選択する必要がある。利用可能なすべての異なるテスト手法を組み合わせて使用することで、構築されたATEを最大限に活用することができます。これにより、すべての製品タイプの試験を成功させるための高レベルのカバレッジを提供しながら、試験を迅速に実行することが可能になります。
手動テストと自動テストの選択
製造量だけでなく、製品のユースケースの全体像を分析することで、正しい道筋は概ね明らかになる。多くの場合、ミッションクリティカルな製品は、正しい動作を保証するために何度もテストされる。そのような製品の例としては、輸送、航空宇宙、医療、防衛産業など、人々の安全を守るために使用されるものや、機能不良が致命的な影響を及ぼす可能性のあるものがある。例えば、航空機部品を製造する企業は、自社製品に欠陥があれば大規模な死や破壊につながることを知っており、そのため自動試験装置に多額の投資を行っている。別の例としては、埋め込み型医療機器のメーカーがある。その製品の品質は、ユーザーの生死を分ける可能性がある。このような企業は、安全上の理由と手頃な価格の両方から、自動テスト技術をいち早く採用しました。自動テストは、疲れることも、調子が悪い日もありません。オペレーターが必要な作業を行う場合、結果は昼食前と昼食後で異なることが示されている。加えて、主観も影響する。ある人には適していても、次の人にはそうでないかもしれない。市場に出すべきでない製品が一般に出回り、却下された製品がまったく問題ないことが証明された。このようなミスは、リコールや修理、ブランドの評判に相当な犠牲を払っている。客観的な限界のもとで作業すれば、結果は常に信頼でき、再現可能なものとなる。
アプリケーションは自動化に適しているか?
手動テストは、テストが単純なプロセスであり、人件費が低い場合に伝統的に使用されている。また、開発中の新製品をテストする際に、柔軟性が重要な要素となる研究開発部門でも、手動テストが頻繁に使用される。テストプロセスを変更し、いくつかの異なるオプションを試すことができるため、手動テストに適している。企業は、ソフトウェア開発にかかるコストが高く感じられるため、手動テストプロセスから自動テストプロセスへの移行が難しい場合がある。
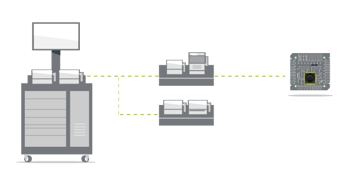
自動テストは、ムーアの法則に従ってテスト機器とソフトウェア・ツールのコストが低下したため、あらゆる種類のエレクトロニクス製品のテストに広く使用されるようになった。テスト装置の価格が下がるにつれて、自動テスト装置の導入が広まっている。また、世界的に人件費が高騰し、手作業によるテストが割高になっていることも、自動テスト普及の一因となっている。専門的なスキルが要求されるニッチな業界では、適切な人材を見つけ、訓練することも同様に費用がかかり、困難な場合がある。自動テストは、大量生産・低価格製品であれ、少量生産・高価値製品であれ、あらゆる製品タイプで使用されている。どの試験装置を使用すべきかを決定する要因は、製造される製品のタイプに依存する。大量生産品や低価格品では、試験時間が重要であることが多いため、製品の試験時間を数秒でも短縮することが、使用する試験装置の種類を選択する際の重要な原動力となります。より複雑で高価値の製品では、多くの試験を深く実施する能力がより重要になるため、試験装置はより洗練されたものになる傾向があり、コストも高くなる可能性があります。
自動化は財務投資に値するか?
新製品の導入に着手する際、ビジネスリーダーが下すべき最大の決断のひとつは、自動テストに投資するかどうかである。自動テスト・システムのセットアップ・コストは、近年下がってきているとはいえ、依然として大きな投資である。とはいえ、いったん初期投資を行えば、それをコスト削減のプラットフォームに変える方法がある。共通のコアを持つテスト・ステーションを設計・導入することで、製造現場での再利用やリサイクルが容易になります。共通のコアや汎用テストステーションの鍵は、高価な計測器をすべてベースユニットにまとめることです。そこから、必要に応じてそれらを入れ替えることで、異なる製品や製品ライフサイクルの段階に対応する柔軟な治具を設計するのは簡単です。
自動化されたテスト機器の導入に対する反対は、組織内部からも起こりうる。既存の従業員の中には、新しいテクノロジーを導入することで自分たちの仕事が脅かされると感じる者もいるからだ。このような脅威の認識は、彼らの仕事の平凡な部分が、ビジネスにより付加価値を与えることができる、よりエキサイティングな役割に取って代わられることを理解すると、しばしば好転する。正しく対処すれば、この状況は関係者全員にとってプラスに転じる可能性がある。
手動テスト、半自動テスト、自動テストの主な違いは説明されたが、どのように決定するかという問題は残っている。
どの戦略がどのような状況に最も適しているかを判断するには、いくつかの質問に答える必要がある:
- 製品は低価格か高価値か?
- 大量生産されるのか?
- テストは複雑ですか、それとも比較的簡単ですか?
- それは最終顧客にとってミッションクリティカルなのか?
- 100%のユニットをテストする必要があるのか、それともバッチテストで十分なのか?
これらの質問に対する答えは、自動テストが導入すべき戦略であるかどうかについて、より適切な判断を下す能力を提供する。低コストでシンプルな電子製品を製造する企業にとって、自動テストは製造とテストのコストを抑えるために不可欠である。このような場合、オペレーターがすべての製品を手作業でテストするのは、あまりにもコストがかかりすぎる。製品が複雑であったり、高価であったりする場合は、製品の複雑さをテストするために必要な専門技術者の人件費が高くつくため、テストを自動化することが理にかなっていることが多い。高価値の製品には、一貫した品質を保証するために、高レベルのテストと文書化されたプロセスを期待する顧客がいることが多い。ミッション・クリティカルな製品では、製造の全段階において、高品質で繰り返しのテストが極めて重要である。テストは、個々のプリント基板のテストからサブシステムのテスト、そして最終的には機能的な受け入れテストに至るまで、アセンブリのあらゆるレベルで実施されなければなりません。このようなタイプの製品の現場での失敗(すなわち、品質不良のコスト)は、包括的なテストよりもはるかに高価です。
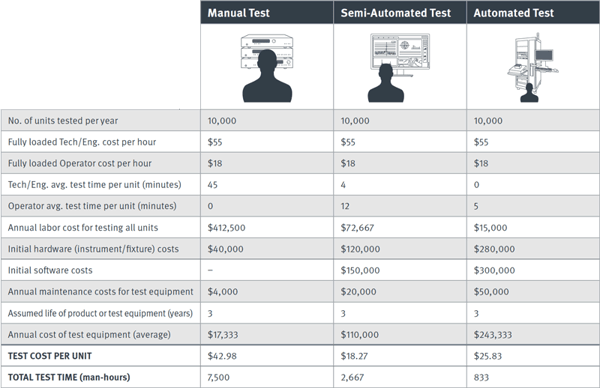
すでに説明したテストプロセスの違いをよりよく理解し、正当化するためには、典型的なテストシナリオの例を当てはめるのが有効である。上述したシナリオ例では、テストが必要な製品を、3つのテストプロセスのそれぞれについて、テストあたりの潜在的なコストで分類している。最良の戦略を決定するために重要な計算は、テスト時間、オペレーターコスト、設備コスト、必要なエンジニアリング開発(すなわち、ソフトウェア設計)である。この例では、固定費、開発費、試験時間の見積もりに従って、ある製品ラインが年間1万台を製造すると仮定している。この情報は、ユニットあたりのテストコストの計算に使用される。この例で重要な費用はテスト時間である。テスト時間が短くなれば、テストあたりのコストは劇的に減少します。
手動試験では、より高い能力が要求されるため、オペレーターのコストは高くなる。訓練を受けた試験技術者が試験を行う必要がある。半自動化または完全自動化された試験シナリオでは、熟練度の低いオペレーターを使用することができるため、このようなことはありません。(このような場合、オペレーターは複数のテスターと同時に作業できる可能性がありますが、この多重化の仮定は計算には使用されません)上表に示した例は、さまざまな試験タイプのシナリオを計算するためのガイドとなります。このケースでは、台数(年間1万台)により、手動テストから半自動テストへの移行は正当化されるが、完全自動テストへの移行は正当化されない。これは、労働コストを大幅に削減するために、何らかの自動化を正当化できるほど十分な数量であるが、完全自動化のより高価なコストを正当化できるほど数量が多くないためである。
製品テストを成功させることは品質にとって非常に重要だが、それにはコストがかかる。製品テストを手作業で行うか自動化するかは、上記のすべての考慮事項を用いて、慎重に検討する必要がある。適切な計画は、効果的な結果をもたらし、全体的な結果を改善しながら製造を加速させる。
さらに詳しく
マシンビジョンと光学検査-アクティブ・アライメント・アセンブリ-テストエンジニアリングの専門知識-RFテスト機器-スマートデータ管理